What are the advantages of MBR membrane in the treatment of printing and dyeing wastewater?
The printing and dyeing industry is a major consumer of water resources and also generates a large amount of complex wastewater. With the increasingly strict environmental requirements, how to efficiently treat printing and dyeing wastewater has become an important challenge faced by the industry. MBR membrane technology, as an advanced sewage treatment method, has shown unique advantages in the treatment of printing and dyeing wastewater.
Application of MBR membrane technology in the treatment of printing and dyeing wastewater
1. Pre processing stage:
Firstly, large particle impurities and suspended solids are removed through grilles and sedimentation tanks. For high concentration dyes and additives in printing and dyeing wastewater, pre-treatment methods such as chemical coagulation precipitation or advanced oxidation can be used.
2. Biological treatment stage:
The MBR bioreactor is the core link. Activated sludge degrades organic matter at high concentrations (8000-12000mg/L) and solid-liquid separation is achieved through membrane separation technology.
3. Membrane separation process:
Using a hollow fiber ultrafiltration membrane with a pore size of approximately 0.1 μ m, it can effectively retain suspended solids, colloids, and most bacteria.
4. Advanced processing:
According to reuse requirements, advanced treatment processes such as activated carbon adsorption or nanofiltration/reverse osmosis can be added.
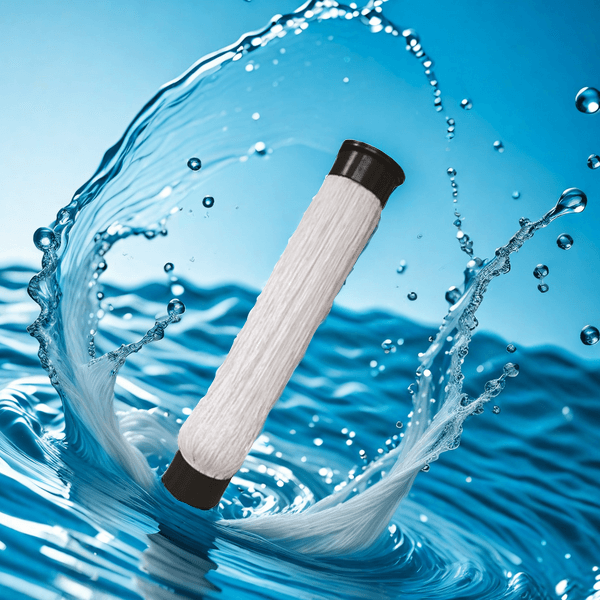
The advantages of MBR membrane technology in treating printing and dyeing wastewater
1. Good effluent quality:
MBR membrane can effectively remove COD, BOD, chromaticity, and suspended solids, and the effluent can meet the reuse standards.
2. Strong resistance to impact loads:
Adapt to the characteristics of large fluctuations in the water quality of printing and dyeing wastewater.
3. Small footprint:
No need for secondary sedimentation tank, compact system, suitable for factory renovation and upgrading.
4. Low sludge production:
Long sludge age operation reduces residual sludge production.
5. Stable operation:
High degree of automation, easy operation and maintenance.
Application precautions
1. Control the incoming water quality:
Prepare well, remove high concentration dyes and additives, and avoid membrane fouling.
2. Optimize operating parameters:
Adjust membrane flux, aeration rate, and other parameters based on the inflow characteristics.
3. Regularly clean the membrane components:
Use chemical or physical cleaning methods to maintain membrane performance.
4. Key monitoring indicators:
Real time monitoring of transmembrane pressure difference, pH value, dissolved oxygen and other parameters.