What are the technological advancements of mbr membrane modules?
MBR is the abbreviation of membrane bioreactor. It is developed on the basis of biological contact oxidation tank. It adds a membrane separation unit on the basis of biological contact oxidation tank. MBR technology has a wide range of applications. At present, MBR technology has been widely used in urban sewage treatment, industrial wastewater treatment, reuse, seawater desalination and other fields, and has achieved good results. Let’s take a look at the advancements in MBR membrane module technology.
1. Selection of membrane
Membrane selection is very important for the operation of the MBR process. It directly affects the treatment effect and service life of the membrane bioreactor. At present, common MBR membrane materials include polyacrylonitrile, polyvinylidene fluoride (PVDF), polysulfone (PSF) and polyethersulfone (PES).
Among them, polyimide (PI) membrane has good biocompatibility, chemical resistance, impact resistance and low temperature resistance. However, because PI membrane is more expensive, it is usually used for industrial wastewater treatment. PSF and PES membranes have good chemical resistance, water resistance, anti-pollution properties, etc., but due to their high cost, they are currently not widely used in industrial wastewater treatment. Polyethersulfone (PES) membrane has good mechanical properties and heat resistance, but has poor chemical resistance and stability. Therefore, it is currently mostly used in the membrane tank of the MBR process.
2. Operating conditions of membrane modules
(1) Incoming water quality: The MBR process has relatively high requirements for the incoming water quality. The concentration of CODCr in the incoming water is required to be 500~1000 mg/L, BOD5 is 300~600 mg/L, ammonia nitrogen is 100~200 mg/L, SS Between 20~50 mg/L, TN is between 10~30 mg/L.
(2) Hydraulic retention time: The operating time of the membrane module is generally about 3 hours.
(3) Membrane module operation mode: Membrane modules generally adopt continuous operation mode, and intermittent operation mode can also be used.
(4) The aeration intensity is generally 10~20m3/(m2.h). When the inlet water concentration is high, the aeration intensity can be appropriately increased to improve treatment efficiency; when the effluent concentration is low, the aeration intensity can be appropriately reduced to reduce energy consumption.
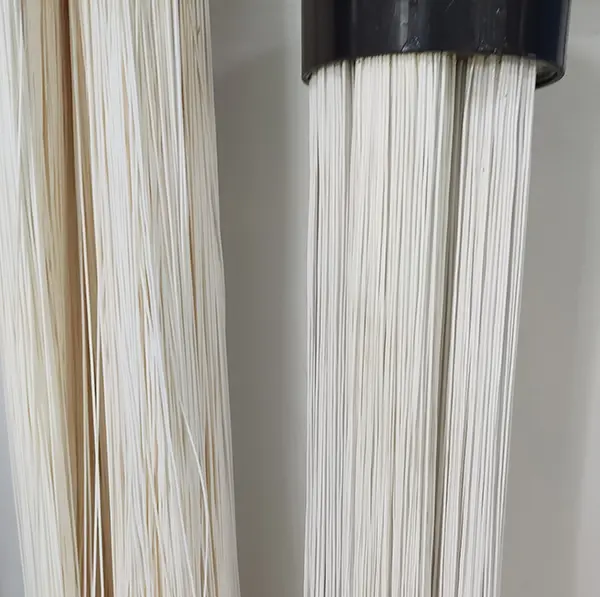
3. Material of membrane module
Membrane module materials are mainly divided into polyvinylidene fluoride (PVDF) membrane, polypropylene (PP) membrane and glass fiber membrane. The better one currently on the market is PVDF membrane, which has high anti-pollution ability, can effectively prevent the deposition of pollutants on the membrane surface, and can effectively increase membrane flux.
4. Improvement of membrane materials
The development of MBR membrane technology is inseparable from the advancement of membrane materials, from traditional PVC membranes to new polymer materials, such as polypropylene hollow fiber membranes, which can better achieve pollutant separation. At present, MBR membrane modules are widely used in wastewater treatment, sewage reuse, food industry, medical and health and other fields. The choice of membrane material directly affects the performance and service life of the membrane module.
5. Membrane fouling and cleaning
MBR technology has broad application prospects, but it also has some shortcomings. One of the disadvantages is membrane fouling. Membrane fouling will affect the quality of the effluent water. In severe cases, it will block the membrane components, causing the system to fail to operate normally. In addition, membrane fouling will also reduce the service life of the membrane. Therefore, in order to make better application of MBR technology, it needs to be cleaned accordingly. Currently commonly used cleaning methods include physical cleaning, chemical cleaning and biological cleaning. Different methods have different degrees of control over membrane fouling. Physical cleaning can be achieved using chemical cleaning agents or ultrasonic methods; chemical cleaning can be used to remove contaminants on the membrane surface.